Meet Customer and Regulatory Requirements with a Quality Management System (QMS)
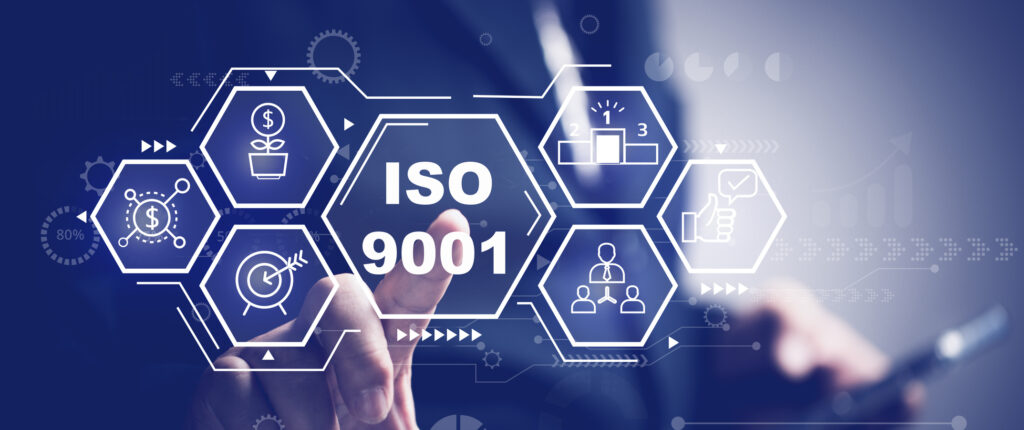
By: Dean Simmons
Many manufacturers utilize a Quality Management System (QMS) in their organizations. A QMS is generally defined as a structured system that documents processes, procedures, and responsibilities for continuously delivering high-quality products and services that meet regulatory and customer requirements.
A popular general quality standard is ISO9001:2015, designed to provide a framework that any organization can use to establish a QMS that is unique to their given industry.
ISO9001:2015
According to the International Organization for Standardization (ISO), ISO 9001 is defined as the internationally recognized standard for Quality Management Systems. It is the most widely used QMS standard in the world, with over 1 million certificates issued to organizations in over 170 countries.
The ISO9001:2015 standard is based on several quality management principles including a sharper risk focus, strong customer emphasis, organizational leadership engagement and participation, process efficiency, and continual improvement. It turns a static set of QMS requirements into a more agile, collaborative, and robust evolving platform.
ISO9001:2015 is a quality management standard for companies and organizations of any size. The standard specifies requirements for a quality management system when a business needs to demonstrate its ability to consistently provide products and services that meet customer, statutory, and regulatory requirements.
The ISO9001:2015 standard also strives to enhance customer satisfaction through effective implementation of processes for improvement and the assurance of conformity to established requirements for any organization, regardless of its type or size, or the products and services it provides.
Key benefits to being certified to the ISO 9001:2015 standard include:
- Improved Quality: organizations can better control their processes, leading to consistent and higher quality outputs
- Customer Satisfaction: regularly delivering products and services that meet or exceed customer expectations often leads to improved customer loyalty and confidence
- Process Improvement: managing and streamlining processes can reduce waste and improve efficiency, which can generate cost savings and increase productivity
- Better Decision Making: The standard emphasizes evidence-based decision making, where organizations can make informed decisions for continuous improvement by collecting and analyzing data related to processes and outcomes
- Risk Management: stronger focus on risk-based thinking helps identify potential issues or concerns that could impact the quality of products or services, with preventive measures to mitigate these risks
- Employee Engagement: employees who understand their roles, responsibilities, and the value of their contributions to the QMS are more likely to be motivated and invested in their work
- Competitive Advantage: many customers view ISO 9001 certification as a commitment to quality and continuous improvement, even opening doors to international markets
- Supplier Relationships: requiring suppliers to meet certain quality management standards can lead to improved relationships as well as consistency and reliability in the supply chain
- Continuous Improvement: following the principles of the standard may lead to ongoing assessment and enhancement of processes, long-term growth, and a company culture of continuous improvement
Management Commitment
ISO 9001:2015, unlike ISO 9001:2008, places emphasis on the proactive, constant commitment of your leadership or management team to the execution of your QMS.
With their renewed dedication and responsibility, your leadership team should:
- Advise everyone in your organization of the importance and benefits of a certified QMS
- Inform your employees why they should participate, and their role, in its implementation
- Ensure your quality policy and objectives align with the strategic plan of your business
- Promote risk-based thinking as it pertains to the organization’s quality management system
- Dedicate adequate resources and guidance to make sure the QMS achieves its intended outcome
Your ISO 9001 auditor will expect to see evidence of management commitment to and responsibility for the quality agenda, including frequent managerial review sessions with documented outcomes.
Quality Essentials Program
CONNSTEP, Connecticut’s Manufacturing Extension Partnership (MEP) center, provides a general overview of Quality Management Systems, including ISO9001:2015 and the aerospace standard AS9100 Rev D, in one of its sessions for its Quality Essentials Program (QEP).
The QEP QMS session defines what a Quality Measurement System standard is, reviews the history of each standard, and provides an understanding of the core elements of each standard. QEP also reviews audit terms and principles used when conducting audits of quality systems adhering to these standards.
It’s important to note that while ISO 9001 offers numerous benefits, successful certification and implementation require commitment, resources, and a thorough understanding of the standard’s requirements. Organizations should carefully assess their readiness and engage in proper planning before pursuing ISO 9001 certification.
CONNSTEP can assist with implementing a new quality standard and/or conducting your standard’s annual audit. Contact us today.
Related Items
Establish a Culture of Quality
Implementing appropriate continuous improvement tools can help establish a Lean culture throughout an entire organization and deliver transformative results.
CONNSTEP’s Quality Essentials Program is being offered to address the growing need to enhance the knowledge of quality principles among skilled manufacturing workers.
[Case Study] Strategic Roadmap Brings Synergy to Growth and Operations
Corru-Seals recognized to fully realize the benefits inherent in the new quality standard would require a paradigm shift in the organization.