Misconceptions of Lean Manufacturing and Continuous Improvement
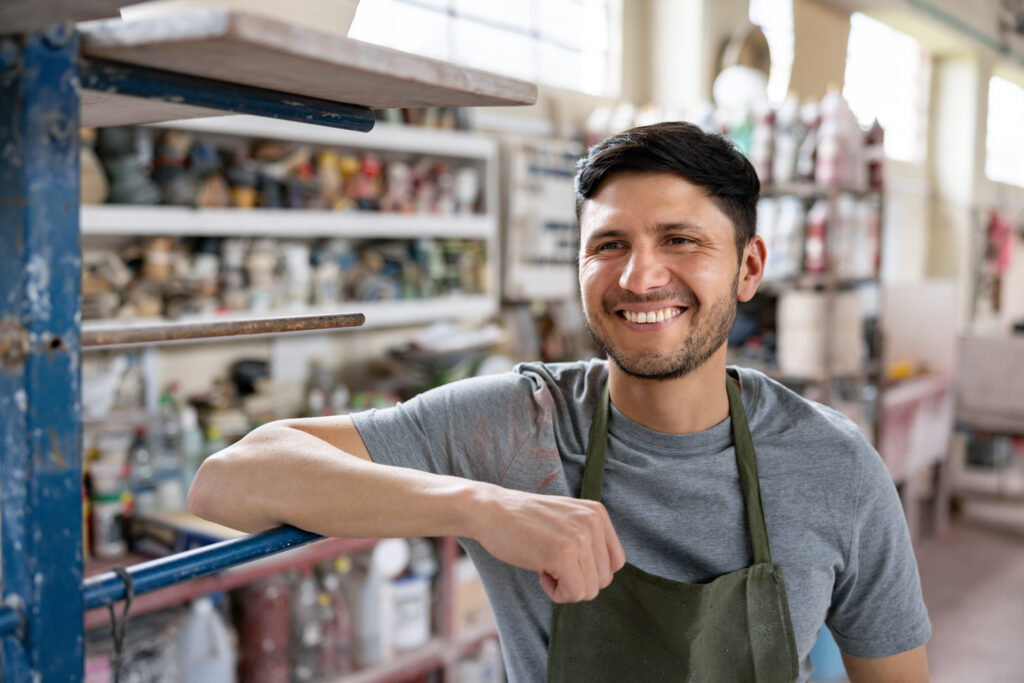
By: Dean Simmons
Lean principles and Continuous Improvement methodologies have garnered significant attention in manufacturing for their potential to optimize processes, reduce waste, and enhance efficiency. However, various misconceptions often cloud the understanding and implementation of these strategies. Let’s explore some of these misunderstandings and uncover the realities of Lean Manufacturing and Continuous Improvement.
Common Misconceptions
One common misconception is that Lean Manufacturing is solely about cutting costs and reducing workforce. While it’s true that Lean methodologies aim to streamline operations and eliminate waste, their primary focus lies in delivering value to customers efficiently.
In their book “Lean Thinking,” authors James P. Womack and Daniel T. Jones emphasize that Lean is about maximizing customer value while minimizing waste across entire value streams. It’s a holistic approach that involves every aspect of the organization, from the production floor to administrative services, with the goal of enhancing quality and responsiveness.
Another myth is that Continuous Improvement is a one-time initiative rather than an ongoing journey. Continuous Improvement is actually deeply ingrained in the culture of Lean organizations. It’s not about just implementing a set of tools and techniques once and then moving on. Instead, it’s a mindset and commitment that encourages employees at all levels to continually seek better ways of doing things, fostering a culture of innovation and adaptability.
Kaizen is a Japanese term meaning change for the better or continuous improvement. It is a philosophy that suggests making small, incremental changes that can add up to significant improvements over time.
Size Does Not Matter
Some may perceive Lean Manufacturing as applicable only to large-scale production facilities, overlooking its relevance to various industries and even small businesses. In reality, Lean principles can be tailored and applied across diverse sectors beyond manufacturing, including healthcare, service industries, and even startups.
Whether it’s reducing lead times in a hospital or streamlining processes in a software development company, the core concepts of Lean—such as identifying value, mapping value streams, and striving for perfection—are universally applicable.
The perception that Lean Manufacturing and Continuous Improvement are rigid frameworks that stifle creativity and innovation could not be further from the truth. On the contrary, these methodologies provide a structured approach that empowers employees to innovate within defined parameters in an organization.
By standardizing processes and eliminating non-value-added activities, Lean frees up resources and time for creative problem-solving and experimentation. It’s about fostering a culture where employees are encouraged to suggest improvements and offer new ideas, driving innovation from the bottom up.
Employment/Workforce Pipeline
Despite a healthy workforce across all three manufacturing sectors, Connecticut has experienced a slight decline in employment in two of the sectors. In aerospace, employment in Connecticut declined by less than half of 1% compared to national growth of just over 1%.
Employment in medical devices in the state dropped just over 1.5% compared to the nationwide decline of just under half of 1%. Conversely, shipbuilding in Connecticut experienced a 4% increase in employment compared to 2% nationally, largely driven by submarine production and maintenance.
Aging and retirement are also concerns for Connecticut manufacturers including those evaluated for the assessment. The good news is that despite the aging of the state’s supplier workforce, new talent continues to enter the aerospace, shipbuilding, and medical devices industries.
Conclusion
Debunking these misconceptions is crucial for organizations aspiring to successfully adopt Lean Manufacturing and Continuous Improvement. By recognizing Lean as a customer-centric approach, understanding Continuous Improvement as an ongoing journey, acknowledging its versatility across industries, and embracing it as a catalyst for innovation, businesses can harness the full potential of these methodologies to achieve sustainable growth and competitive advantage.
Continuous Improvement Champion Certification (CICC)
This course provides comprehensive exposure to the principles and practices needed to develop and sustain a Lean Enterprise. You will receive immediate reinforcement of the classroom learning by applying your training to a real-life project within your organization.
Often basic housekeeping is overlooked in favor of “productivity.” This is a common practice but one that costs you over the long run. Putting a basic 5S program in place is inexpensive and yields a great return on your (small) investment.
[Case Study] Improvement to Process Flow Increases Productivity
By enrolling an employee in CONNSTEP’s CICC program, the company streamlined their workflow, resulting in significant operational gains and reduced lead times, ultimately enhancing their overall performance