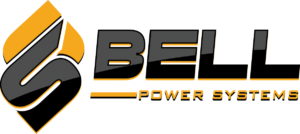
Continuous Improvement Training Facilitates Flow Line Adjustments for Higher Volume Builds
Bell Power Systems (BPS) was founded in 1967 as Bell Detroit Diesel and in 2012 became part of the Superior Diesel family of companies. They specialize in providing value-added diesel engine packages, service parts, and drivetrain components to original equipment manufacturers and dealers for off highway equipment applications for a territory covering the eastern United States.
The company maintains an inventory of 700 to 900 engines ranging from 4 to 600 horsepower at their 60,000 square foot manufacturing and warehousing facility in Essex, Connecticut. BPS serves industries that include pumps, aircraft ground support, agriculture, marine propulsion, railroads, oil and gas.
Executive management at Bell Power Systems had previous exposure to lean manufacturing and wanted to expand the continuous improvement (CI) focus at their facility. BPS had recently promoted shop floor employee Bob Green to Production Supervisor to advance their lean operations.
To take advantage of Green’s previous shop floor experience and leverage continuous improvement practices, BPS sought out lean training opportunities for Green with the intent of improving both production line efficiencies and lead times. BPS reached out to CONNSTEP who recommended its Continuous Improvement Champion Certification (CICC) training program for Green to attend.
During the CICC course and subsequent to its completion, Green began employing Lean manufacturing tools and techniques at BPS. Referencing their production line current state value stream map and future state material flow, he cross-trained many employees and shared the benefits of Lean manufacturing principles and processes.
To help gain production line efficiencies and shorten lead times, spaghetti diagrams were drafted to provide a visual representation of the continuous flow line showing the path and locations of parts and inventory for optimum access and use within the manufacturing facility and warehouse. Additional changes were made to other areas to streamline efficiencies.
The implementation of Lean manufacturing practices resulted in improved flow line for production with higher volume builds. Parts, racking, and engines were moved closer to employee workstations reducing feet traveled from 4131 to 2314. 5S auditing sessions were conducted to continually update work instructions and evaluate inventory locations. Total cycle time was reduced by 18% with an ultimate goal of a 20% reduction.
Ergonomic workbenches were created to make them more accessible and efficient to use. Work instructions were updated and improved, with pictures added to help in cross training load leveling to better meet customer demands and expectations. On-time delivery improved from 92% to 100%. Over a 17-month period, the BPS Essex location improved their efficiency tracking rate (sales/hours) from 75% to 185%.
The continuous improvement lessons learned from CONNSTEP really helped our shop. Just moving 85-90% of our inventory and grouping parts closer to employee work areas has saved hours of work.
Bob Green, Production Supervisor, Bell Power Systems
Project Impact
Want to achieve results like these?
Related Items
Often basic housekeeping is overlooked in favor of “productivity.” This is a common practice but one that costs you over the long run. Putting a basic 5S program in place is inexpensive and yields a great return on your (small) investment.
Continuous Improvement Champion Certification (CICC)
This course provides comprehensive exposure to the principles and practices needed to develop and sustain a Lean Enterprise. You will receive immediate reinforcement of the classroom learning by applying your training to a real-life project within your organization.
[Case Study] Enterprise-Wide Lean Transformation Drives Growth & Revenue
“The enterprise-wide lean transformation facilitated by CONNSTEP helped give us the continuous improvement head start we needed."